Экономный и надежный пол: как одновременно снизить себестоимость и повысить качество.
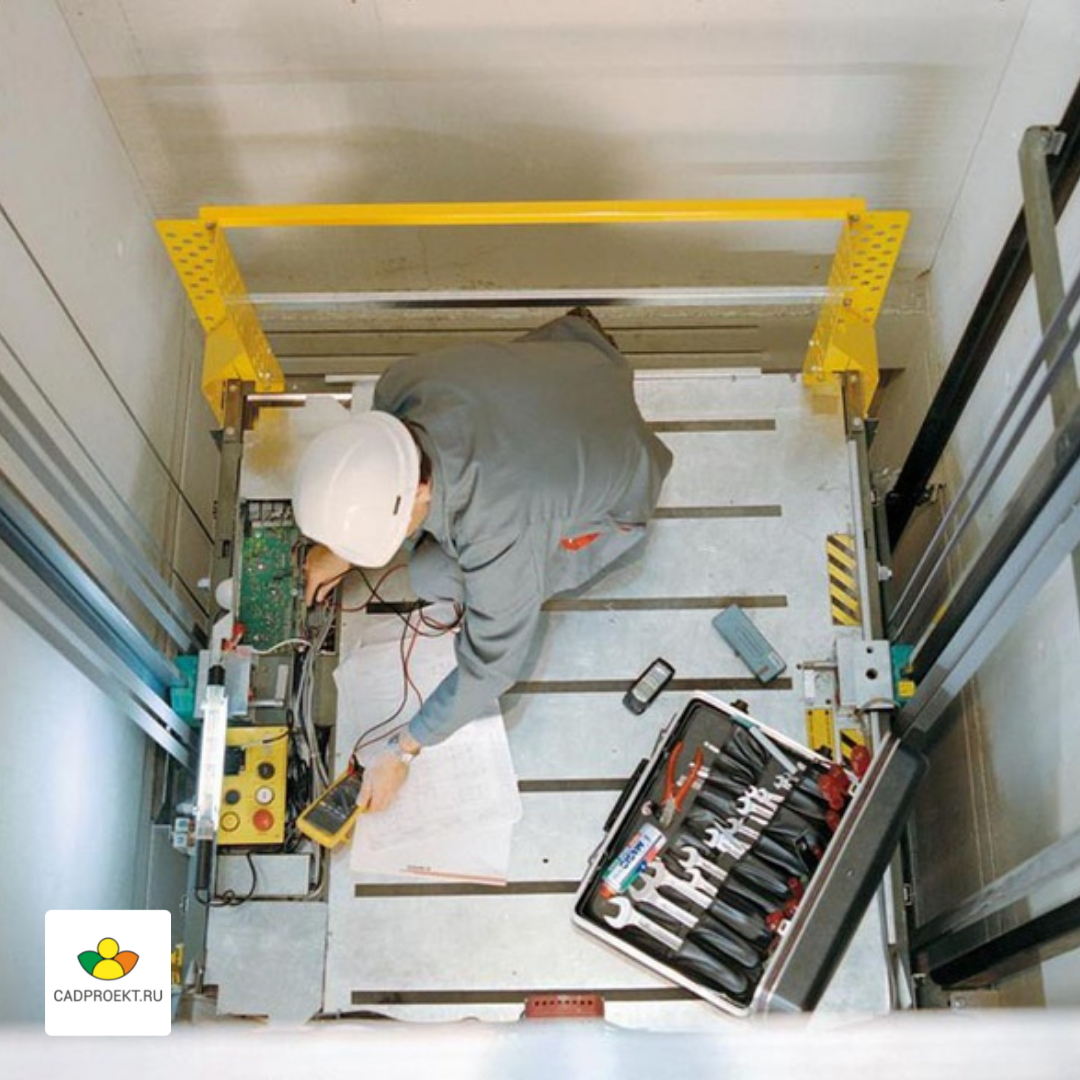
«Экономия должна быть не только экономной, но и качественной!»
© CADPROEKT.RU
Долговечная и качественная продукция, выпущенная с минимальными затратами – мечта любого производителя! Порой в стремлении к этому идеалу, разработчики и изготовители идут на жертвы: увеличивают вложения в надежде дороже реализовать товар либо, наоборот, заменяют дорогие материалы более дешевыми и продают продукцию дешевле аналогов - зарабатывают не на качестве, а на количестве.
Но экономия ДОЛЖНА и МОЖЕТ быть со знаком качества! Об одном таком случае из своей практики рассказал ведущий инженер-технолог CADPROEKT.RU Денис Лазовский.
– На лифтовом производстве активно работали над совершенствованием пола кабины лифта. Если точнее – над технологией приклеивания напольного покрытия к настилу рамы пола. Чтобы увеличить производительность и снизить себестоимость этого процесса, решили заменить один клеящий материал (клей 88-СА) на другой (аэрозольный клей Super -77).
Замена была необходима по нескольким причинам. Использование 88-СА было довольно трудоёмким: клей наносили кисточкой в два слоя с выдержкой между слоями 5-15 минут, а потом удерживали под нагрузкой не менее 60 минут! А еще этот материал был небезопасным из-за выделяемых в рабочую зону вредных веществ. То есть для налаженного рабочего процесса нужны были дополнительные средства на покупку респираторов и установку системы вытяжной вентиляции.
– Когда 88-СА заменили на аэрозольный клей Super 77, получилось значительно повысить производительность процесса. Общее время на нанесение, выдержку перед склейкой и прижатие склеиваемых поверхностей сократилось более чем в 2 раза.
Казалось бы, оптимизация случилась, но… с разных объектов, куда поставлялись эти кабины, начали приходить рекламации об отклеившемся или съехавшем напольном покрытии. Ситуацию надо было срочно исправлять!
Перед инженером-технологом встала непростая задача: найти материал, который, как минимум не увеличил бы трудоемкость изготовления изделия, а как максимум – решал вопросы безопасных условий труда и давал заметный экономический эффект.
– Какой из способов нанесения материала на поверхность быстрее аэрозольного вы знаете? У меня даже предположений не было на этот счет. Не говоря уже про решение задачи «максимум». Анализируя и подбирая продукт, я понимал, что альтернативы нет: то время не устраивало, то технология применения, то цена, то качество не внушало доверие… Однако мучительные поиски, переговоры с различными поставщиками и производителями клеев, в конце концов, дали результат.
Один из представителей производителей клеев предложил использовать двухкомпонентный клей на основе полиуретана (Макропласт УК 8103). Данный материал поставлялся в двух емкостях (ведра по 6 кг и 24 кг) в объемном соотношении 1:4 (соответственно компонент «А» - отвердитель, компонент «Б» - клей).
Клей был:
- безопасным (средства защиты были не нужны)
- качественно приклеивал напольное покрытие
- приемлем по стоимости
– Но вопросов по прежнему было больше, чем ответов: процесс приклеивания покрытия казался слишком долгим и даже нереалистичным. Было непонятно, чем смешивать клей, как именно смешивать (нужно было соблюсти пропорцию), в каком объеме мешать (на какую партию изделий, ведь сменно-суточные задания каждый раз разные и могут изменяться в процессе производства), и что делать с остатками неиспользованного замешанного клея (жизнеспособность клея составляла 40 минут).
Но на то технологи и технологи, чтобы любой подобный ребус разгадать.
Итак, чтобы не увеличивать трудоемкость, не загромождать процесс побочными операциями типа первоначального смешивания компонентов в емкости, нанесения готовой смеси на настил рамы пола и т.д., решили вот что:
– Мы высчитали количество клея на одно изделие и определили объем мерных емкостей для каждого из компонентов в расчете на одно изделие, при смешивании которых получалась бы требуемая пропорция. Также сформировали заявку на изготовление мерных емкостей.
Сам процесс должен быть выглядеть так:
- мерными емкостями оба компонента клея наносятся из ведер сразу на настил рамы пола;
- затем при помощи обычного строительного шпателя одновременно необходимо размешать и распределить компоненты клея по всему настилу рамы пола (т.к. компоненты клея довольно жидкие, проблем это не вызвало, штукатурам-отделочникам надо было просто привыкнуть – освоились быстро);
- следом – укладка и приклейка напольного покрытия к настилу рамы пола без дополнительного времени на выдержку, чтобы нанести второй слой и прижать. Этого не требовалось, т.к. клей обладал хорошей адгезией, достаточной для предотвращения смещения напольного покрытия. Окончательное схватывание происходило в процессе дальнейшей сборки лифта в течение 2-3 часов. Полная полимеризация клея наступала через сутки.
Благодаря такой технологии отпали вопросы о необходимости тары для смешивания, остатков и возможных отходов готовой смеси. Делалось все оперативно, в нужном количестве и по месту.
Процесс нанесения двухкомпонентного клея, конечно, был более трудоемким в сравнении с аэрозольным вариантом. Но за счет сокращения затрат на выдержку для нанесения второго слоя и прижатие удалось сохранить паритет в производительности процессов. А за счет меньшей стоимости клея (с учетом расхода на единицу продукции) была и экономическая выгода от внедрения данной технологии.
После успешных испытаний новый способ внедрили в производство. Желаемый результат достигнут: расходы меньше, качество лучше, производительность труда увеличилась. И самое главное – клиенты довольны!