Нюх на нестандартные решения.
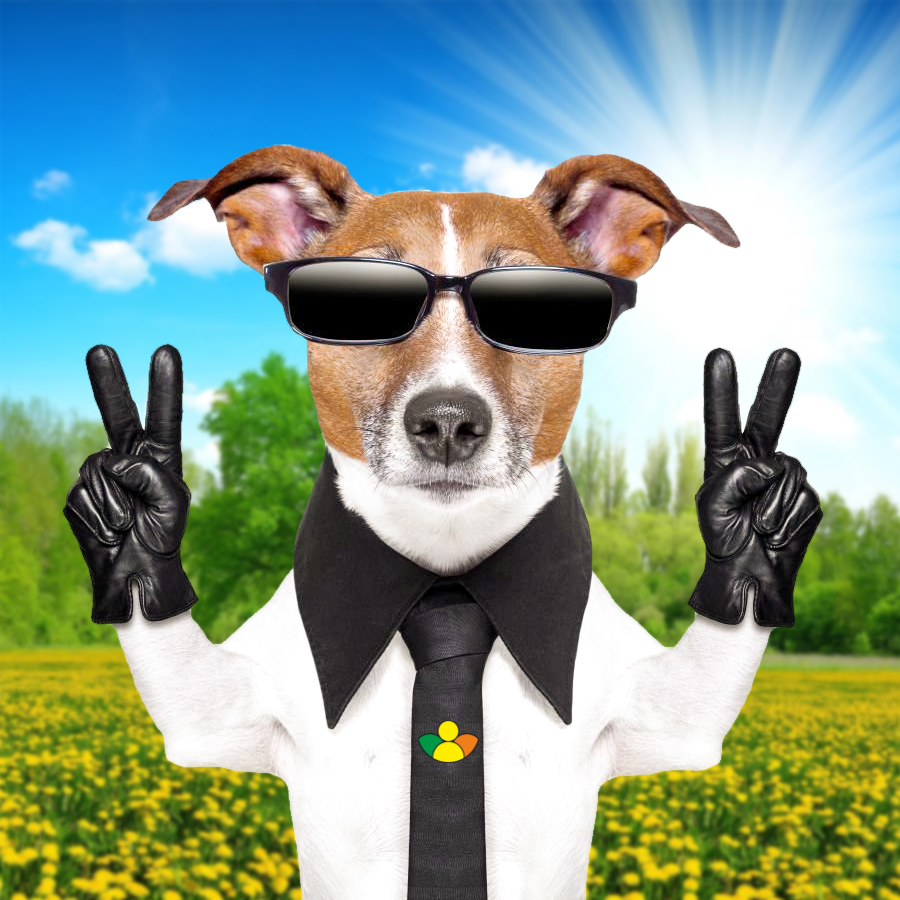
Нет! Мы не призываем напрочь забыть матчасть и руководствоваться одной лишь интуицией. Тем более в проектировании. Мы предлагаем сочетать фундаментальные знания и творчество. И как только вы овладеете этим мастерством, придет тот самый нюх на нестандартные решения.
Вот очередная история от нашего ведущего инженера-технолога Дениса Лазовского.
– В прошлый раз я рассказывал, что много лет проработал на лифтовом производстве. Одной из моих обязанностей тогда была проверка сборки ловителей кабины лифтов. Это элемент безопасности, от исправности которого зависят здоровье и жизнь людей. Узел состоит из нескольких компонентов. Один из них – колодка в сборе – особенно меня интересовал. На первый взгляд – это простой узел. Но он требует максимальной точности и качества изготовления.
Технология сборки ловителя изначально была такова: колодка и две щеки собираются между собой при помощи заклепочного соединения. Заклепки – обычные стальные с потайной головкой (всего 4 штуки). Вся трудность заключалась в том, что между щеками, которые устанавливались по обе стороны колодки, должно быть определенное расстояние, которое ни в коем случае нельзя нарушать. А внешние стороны (с которой устанавливаются заклепки) должны быть гладкими – без выступа головок заклепок, заусенцев, забоин и прочих дефектов.
– Проблема в том, что клепали вручную, молотком. От того и качество страдало и погрешности были. Часто приходилось доводить сборочный узел до совершенства при помощи напильника. Такое положение дел не устраивало ни меня, ни особенно рабочих, которые изготавливали этот узел. Орудовать молотком на производстве в 21 веке?! Ну уж нет! Нужна механизация! Причем с минимальными затратами.
Идея приобрести специальное оборудование даже не рассматривалась. Любой станок – уже значительные затраты. А бюджетом такая покупка не предусмотрена.
– Концепция модернизации технологии пришла неожиданно, когда в цеху мне на глаза попался гидравлический пресс. Почему бы не использовать его для клепания так же, как при запрессовке деталей? Я изготовил простую оснастку для обжатия заклепок, подготовил узел, установил на пресс, произвел обжатие заклепок (сразу всех 4-х).
Первый результат оказался некачественным – заклепки до конца не обжались. Шляпка со второй стороны заклепки не получилась, остались «торчащие хвосты», а заполнение предварительно выполненного углубления (цековки) под шляпку не произошло.
– Я предположил, что не хватило усилия: пресс был на 20 тонн. Решил повторить эксперимент, только уже с двумя заклепками. Снова обжатие, и… результат совсем иной – неразъемное соединение вышло отличным! Головки заклепок получились заподлицо с обеих сторон, никаких вмятин и забоин от молотка на щеках, даже не понятно было, с какой стороны происходило формирование второй шляпки заклепки.
Следующим шагом было определение необходимого усилия и, соответственно, оборудования для обжатия сразу 4-х заклепок. Недолго думая, я нашел в цеху такой же гидравлический пресс, но на 40 тонн. Снова проверка опытного образца. И первая же попытка оказалась успешной!
В виду малой загруженности пресса в производстве, решение о переводе изготовления колодки в сборе на данное оборудование было принято моментально. Также был разработан и изготовлен комплект полноценной оснастки под пресс для обжатия заклепок.
Желаемый результат был достигнут. Удалось получить не только качественное заклепочное соединение, но и решить ряд задач:
- механизировать процесс изготовления колодки в сборе с минимальными затратами;
- улучшить качество изготовления сборочного узла;
- повысить производительность процесса (операция клепки на прессе стала занимать лишь несколько секунд).
Так что, инженеры-технологи, чаще заглядывайте в цеха и под разными углами смотрите на оборудование. Как видите, иногда можно самостоятельно расширить его функционал с пользой для производства.